String
instruments have three main parts:
1)
the body, where the sound's resonance is produced,
shaped and intensified;
2)
the neck, which has stretched strings that pass over
the resonant body-these strings are pressed down with
the fingers of the left hand in order to produce sounds
of various pitches; and
3)
the head, which has pegs that hold the ends of the
strings and are used for tuning the instrument.
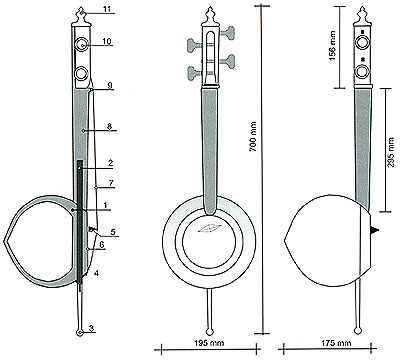 |
1.Body.
2.Pivot. 3.Stand. 4. String holder. 5. Big stand.
6. Back
7. Strings. 8.Neck. 9.Small stand. 10. Pins. 11.Head. |
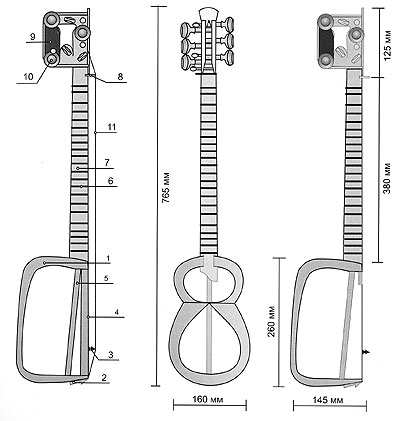 |
1.Body.
2.String holde. 3. Bi stand. 4. Back. 5.Pivot.
6.Frest.
7. Neck. 8.Small stand. 9.Head. 10. Pins. 11.
Strings |
There
are two types of technology for making the body of
a string instrument:
1) A method of assembly in which the various parts
of the instrument are made separately and then put
together. The ud, saz, barbat, choghur, chagane, santur
and ganun are made in this way.
2) A method of hollowing out a tree stump from the
inside and polishing it from the outside to create
the required form. The tar, kamancha, rud, rubab,
tanbur, gopuz and chang are made in this way.
For the first method, first a special form is made.
An element called a "kup" is placed on the
upper part, and another called a "dabanjig"
is placed on the bottom of the form. Dried wood is
cut into five-mm-thick lags of the appropriate sizes.
These lags are soaked in hot water (70-90 C) for 20-25
minutes, bent in the form and installed on the kup
and dabanjig.
The lags are fixed with the help of metal clips. The
number of lags is usually odd (9 or 1 1).
Next, the neck is fixed to the finished body. It is
important to make sure that the body corresponds to
the neck. There should be a five-mm gap at the juncture
of the body and neck. This gap is left to fix the
neck in position after straining the strings. A special
rule is used to be exact in defining this space.
After fixing the body and neck together, the sounding
board is added. The sounding board is made of mulberry
or nut wood. The thickness of the sounding board is
five mm. It is greased with linseed oil or another
vegetable oil and left for several days. Once the
wood absorbs the oil completely, it is dried on the
fire. Several days later, this procedure is repeated
again. The finished sounding board is attached to
the body using special wood glue made from cod liver
oil. Separate pieces are polished and cleaned. Then
a hot glue is placed on them. The parts are assembled
and tightly pressed together. Next, pegs and frets
are fixed to the instrument.
For the second method, the artisan has to take into
account the season in order to determine when the
tree should be cut down. The trees' level of gumminess
usually goes down in January and February. The tree
has to be cut down at this time, since a body made
of wood with a high gum level always chaps or warps
after drying. After the body is hewed out, it should
be allowed to dry.
In order to make the body of the instrument, the tree
trunk that is cut out should be bisected and the core
should be taken out. The surfaces of the two pieces
are polished. Then, the contours of the instrument
are drawn on the pieces so that they can be hollowed
out along these contours. The mulberry tree should
be hollowed out when the wood is still wet. Practice
shows that an old and cored tree is not good for making
the body of a music instrument.
The sounding of the instrument depends greatly on
how it has been assembled. After the body is dried,
the inner and outer parts are hewed and polished again.
Then the neck, head and other parts of the instrument
are fixed to the body. A film made from bull heart
or fish skin is stretched over the body. A large bridge
situated inside the body receives the vibration of
the strings and transfers it to the inner cavity of
the body. The acoustic waves that are generated in
this cavity flow out again. The sound becomes louder
and longer as this process repeats, giving the sound
a nice full timbre.
It is necessary to draw special attention to the solidity
of the wood used to make the neck, because this area
may bend under pressure while the instrument is being
tuned. The pear tree is the best for making pegs.
Pear wood pegs sustain the atmospheric pressure better
and stay in tune.
The strings are made of metal, kapron, silk or animal
gut. Metal strings produce the strongest and clearest
sound. However, they are much more difficult to press
with the fingers than silk or gut strings are. The
thickness of the strings depends on the individual
instrument. The loops on the ends of these strings
(photo) are inserted into the tailpiece on the lower
lateral part of the body. The tailpiece is made of
metal, ebonite or another firm wood.
The instrument-making traditions established in Azerbaijan
by talented craftsmen in olden times are still alive
today and are followed by dozens of contemporary professional
and skillful instrument makers. |